Table Of Content
There are a few basic and standard warehouse floor plans—U-shaped, I-shaped, and L-shaped. Plus, their easy-access design makes them an efficient alternative to stocking small goods in closed boxes, and they can be easily color-coded. The name is a bit deceiving, as pallet racks generally hold more weight than HD shelving. Pay attention to the weight ratings on the shelves you purchase; for safety reasons, it’s important to adhere to weight stipulations assigned by the shelving unit’s manufacturer. Once you have calculated your storage space, the next step would be to plot your workspace and plan for equipment.
Warehouse Layout Design FAQs (Frequently Asked Questions)
How Industry 4.0 is Interwoven into Modern Warehouse Design - SupplyChainBrain
How Industry 4.0 is Interwoven into Modern Warehouse Design.
Posted: Thu, 04 Jan 2024 08:00:00 GMT [source]
This step is dedicated to instilling the essence of flexibility, ensuring that the warehouse can seamlessly adapt to changes in inventory volume, operational processes, and emerging industry trends. In conclusion, Step 7, the Integration of Technology, is pivotal in transforming warehouses into technologically advanced hubs of operational excellence. Warehouse Management Systems (WMS), automation solutions, and the promise of future technologies like AI and IoT collectively contribute to heightened efficiency, accuracy, and adaptability. The strategic implementation of technology ensures not only current optimization but also prepares the warehouse for the dynamic landscape of technological advancements. As we progress through the strategic steps of designing an effective warehouse layout, Step 5 focuses on the paramount task of harnessing vertical space.
Step 1: Comprehensive Inventory Assessment
From mapping out the layout to selecting the right equipment and testing the plan, each step plays a vital role in achieving an optimized and well-functioning warehouse. The U shape is used to keep major warehouse traffic flow separate and streamlined. Keeping the incoming and outgoing materials on parallel sides of the operation helps to avoid bottlenecks. This flow of goods is also helpful in minimizing the available space necessary.
Bulk Storage Layout
The collaborative dance between humans and robots creates a dynamic synergy that amplifies overall operational efficiency. The precision of Pick to Light lies in its ability to reduce cognitive load on warehouse staff. Visual cues direct pickers to the right locations, eliminating guesswork and enhancing accuracy. This precision extends to batch picking scenarios, where multiple orders can be fulfilled simultaneously with orchestrated efficiency.
Step 2: Space Evaluation
Implementing a culture of continuous improvement is essential for sustained workflow efficiency. Regularly assess and reassess the design, seeking feedback from the operational staff, and leveraging performance metrics. Implementing Warehouse Management Systems (WMS), RFID technology, and real-time tracking can provide invaluable insights into the movement of goods. This data-driven approach allows for proactive decision-making and adjustments to further optimize the workflow. Maximizing vertical space aligns with principles of environmental sustainability. By making the most of existing warehouse space, businesses can minimize the need for land expansion, contributing to reduced environmental impact and resource consumption.
Plan for Space Optimization
U-shaped warehouses are good general designs that work for a large number of situations. L-shapes help reduce back-and-forth movement, which is helpful for large products and controlling traffic flow. The best warehouse design for your business really depends on a number of factors.
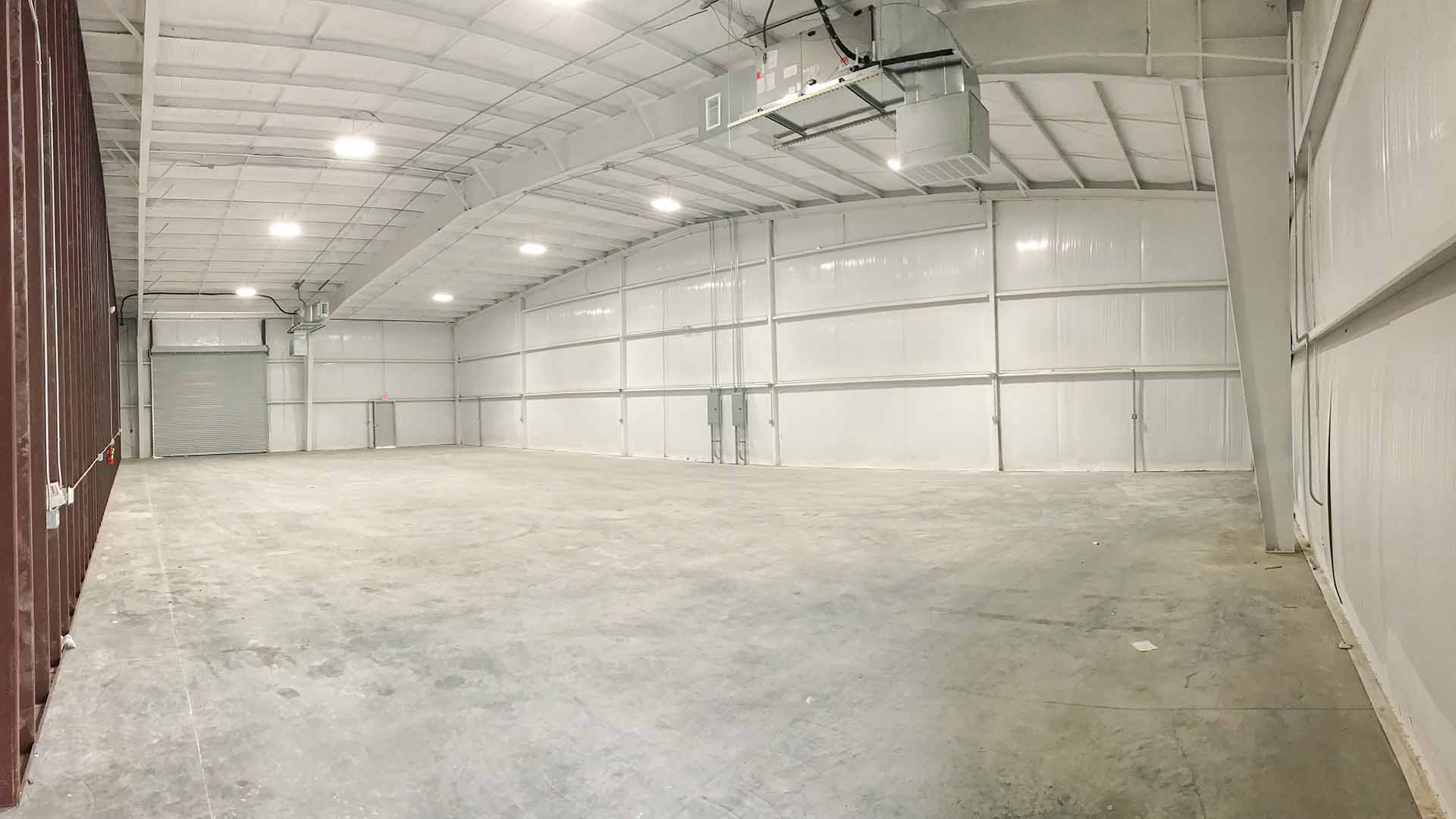
Decisions Guided by Strategic Storage Zones
While designing your warehouse layout, it is critical to comply with the guidelines provided by the local authorities. Abiding by these guidelines not only ensures the safety of your workers, equipment, or other valuable assets but also helps you avoid fines and legal problems for your business. It’s important to make sure your warehouse’s layout does not impede the movement and productivity of your employees. The layout should also be designed while keeping the future in mind — you should have enough space so new employees, products, and materials can be added comfortably down the line.
This exploration delves into the intricacies of each technology, unraveling the symphony that propels order picking into a new era of speed, precision, and operational excellence. The integration of these systems creates a unified platform for real-time monitoring, data analytics, and control. WMS integration enhances visibility into warehouse operations, facilitating informed decision-making and optimization. As the warehouse evolves and business dynamics change, the selected technologies should adapt seamlessly to increased demands. Future-proofing the warehouse layout ensures that investments in automation continue to yield returns over the long term. In the realm of bulk storage, pallet shuttles shine as architects of efficiency.
The reception or staging area is crucial in receiving deliveries, implementing quality control, and initiating product sorting. Designate a separate and spacious reception area to prevent bottlenecks during unloading. A clear separation ensures accurate product inspections and provides ample space for sorting activities. A forklift, ideal for indoor work and transporting heavy items, requires wider aisles (12-13 feet), while pallet jacks, used for shorter distances, provide more flexibility.
This information serves as the canvas upon which the entire layout will be crafted. The insights gained from the inventory assessment form the basis for developing an informed layout strategy. By knowing the unique attributes and demand characteristics of each product, you can strategically position items within the warehouse for optimal efficiency.
With Matterport’s Facilities Management features, capture your building in photo-realistic 3D to create a virtual version of your warehouse. The digital twin includes accurate measurements of the interior, exterior, and exact dimensions of all your equipment. From there, use virtual staging to make design modifications to your floor space. For example, you want to try out a U-shaped design, but after staging, you find that your aisles don’t have enough clearance for materials handling equipment like forklifts. You’re then able to change it up to find a layout that works better for your space with the convenience of a digital model. But following some basic principles of efficient warehouse layout can guide you through this sometimes stressful design process.
Implementing visual cues contributes to a proactive safety culture within the warehouse. Technology is not static, and neither should be its integration within the warehouse. Continuous monitoring of system performance, regular software updates, and the incorporation of new features are essential. This proactive approach ensures that the warehouse stays ahead of the curve in technological advancements. Although every warehouse owner and manager has unique needs for their layout, they often use the same starting point.